When Bigger Isn’t Always Better
With the advent of the mega ships such as Panamax and the Ultra Large Container Vessels (ULCV), shippers and logistics experts were all so excited. The thought of one ship holding 10,000 TEUs, 14,500 TEUs or even more promised untold efficiencies. This supersizing of shipping seemed like a universal advantage for everyone in logistics, economies of scale – multiplied. The reality has been somewhat different.
Container Mania
In the last decade, the number of containers per ship has doubled, tripled in some cases. This increased capacity for necessitated improvements in the supply chains worldwide. Ports have had to add cranes, upgrade software, and improve systems. Many corporate alliances have formed around the globe to make infrastructure improvements such as expanding the Panama Canal and studying a potential Nicaraguan canal. The increased capacity in one area of the supply chain, shipping, has both necessitated and inspired innovation and cooperation.
Nevertheless, the ability to build big ships is outpacing our ability to integrate them into the existing global supply chain. Supersizing shipping generates volume discounts in that industry but creates issues in the overall system. Bigger ships with more containers mean fewer sailings. Less frequent sailings mean less flexibility to market. Just in Time business processes have to be re-calculated. Lean Supply Chains must factor in safety stock and the added warehousing expenses.
Calling All Logistic Experts
Doubts about sustainability and resilience in the logistic models surface. (Never a dull moment in logistics.) This supply chain chaos threatens our customers “Amazon effect” readiness and lowest cost, best value strategies. They turn to us, the transportation experts, who have spent years learning lean processes, eliminating excess and inefficiencies, and engineering for level volumes and core competencies to deal with this dilemma.
Based on the demand, it appears that ULCVs are here to stay, redefining the scale. Every aspect of the supply chain, from infrastructure to personnel to software and systems, must change. But change takes time.
At the IANA conference in September of 2018, major importers and exporters complained about the effect that SuperSized shipping was having on global supply chains. The ULCVs save the shipping companies money by reducing their number of trips. However, they also reduce the frequency of ships, which introduces additional lag time. Then these 14,500+ TEU ships overload the supply chain partners at the port because they are not set up to handle the capacity. This results in
- missed deadlines
- not enough chassis
- longer dwell times costing storage
- warehouse and DC overwhelm
- stock outages
- missed appointments followed by truckers calling for work…root cause could the bigger ships coming less often.
Take Action
As Supply Chain specialists and Logistics experts, it’s our duty to manage this issue with regard to both the infrastructure and the customer experience. I challenge/advise you to have a conversation with your partners. Plan ways to sustain their businesses between the large vessel arrivals. Help them devise a solution that provides continuous service level for your warehouse, and minimizes per diem, storage, overtime. There are lots of options. But it’s going to require everyone in the transportation industry to work together to refine Just In Time processes and create Lean Supply Chain 2.0.
My ask is that we plan for success together and realize we are all working with new challenges requiring new solutions.
Supersize Shipping
With the advent of the mega ships such as Panamax and the Ultra Large Container Vessels (ULCV), shippers and logistics experts were all so excited. The thought of one ship holding 10,000 TEUs, 14,500 TEUs or even more promised untold efficiencies. This supersizing of shipping seemed like a universal advantage for everyone in logistics, economies of scale – multiplied. The reality has been somewhat different.
Container Mania
In the last decade, the number of containers per ship has doubled, tripled in some cases. This increased capacity for necessitated improvements in the supply chains worldwide. Ports have had to add cranes, upgrade software, and improve systems. Many corporate alliances have formed around the globe to make infrastructure improvements such as expanding the Panama Canal and studying a potential Nicaraguan canal. The increased capacity in one area of the supply chain, shipping, has both necessitated and inspired innovation and cooperation.
Nevertheless, the ability to build big ships is outpacing our ability to integrate them into the existing global supply chain. Supersizing shipping generates volume discounts in that industry but creates issues in the overall system. Bigger ships with more containers mean fewer sailings. Less frequent sailings mean less flexibility to market. Just in Time business processes have to be re-calculated. Lean Supply Chains must factor in safety stock and the added warehousing expenses.
Calling All Logistic Experts
Doubts about sustainability and resilience in the logistic models surface. (Never a dull moment in logistics.) This supply chain chaos threatens our customers “Amazon effect” readiness and lowest cost, best value strategies. They turn to us, the transportation experts, who have spent years learning lean processes, eliminating excess and inefficiencies, and engineering for level volumes and core competencies to deal with this dilemma.
Based on the demand, it appears that ULCVs are here to stay, redefining the scale. Every aspect of the supply chain, from infrastructure to personnel to software and systems, must change. But change takes time.
At the IANA conference in September of 2018, major importers and exporters complained about the effect that SuperSized shipping was having on global supply chains. The ULCVs save the shipping companies money by reducing their number of trips. However, they also reduce the frequency of ships, which introduces additional lag time. Then these 14,500+ TEU ships overload the supply chain partners at the port because they are not set up to handle the capacity. This results in
- missed deadlines
- not enough chassis
- longer dwell times costing storage
- warehouse and DC overwhelm
- stock outages
- missed appointments followed by truckers calling for work…root cause could the bigger ships coming less often.
Take Action
As Supply Chain specialists and Logistics experts, it’s our duty to manage this issue with regard to both the infrastructure and the customer experience. I challenge/advise you to have a conversation with your partners. Plan ways to sustain their businesses between the large vessel arrivals. Help them devise a solution that provides continuous service level for your warehouse, and minimizes per diem, storage, overtime. There are lots of options. But it’s going to require everyone in the transportation industry to work together to refine Just In Time processes and create Lean Supply Chain 2.0.
My ask is that we plan for success together and realize we are all working with new challenges requiring new solutions.
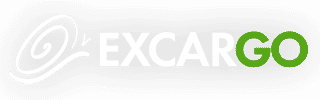
Stay Connected with Us!
Corporate Address
2080 Genoa Red Bluff Rd, Houston, TX 77034
Warehouse Facility
4300 Malone Dr, STE 100, Pasadena, TX 77507
Yard Facility
9888 Wallisville Rd, Houston, TX 77013

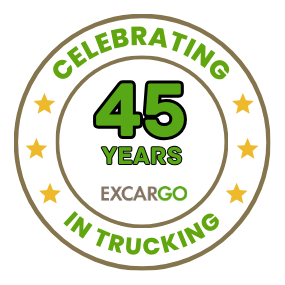